Customer Success Story
Chropynska Slovakia –
When augmented reality means efficiency
Chropynska Slovakia is an engineering and manufacturing company based in Detva, Slovakia. The company’s production program consists of turnkey automated welding and manufacturing lines and production equipment for various industries, including automotive, aerospace, rail, and agriculture. By adopting Twyn, Visometry’s augmented reality solution for visual quality inspection, Chropynska Slovakia has sped up its processes and reduced errors and costly rework.
In any metallurgical process, whether it concerns the production of cars, trains, ships, or airplanes, welding still plays a central role today. It is a process that requires precision and maximum accuracy, and it has been transforming in recent years by introducing automation concepts even where, until not long ago, manual processes were the norm. Furthermore, the lack of specialized personnel is increasingly pushing towards automation and robotization, which, however, require tailor-made equipment and accessories to yield concrete results.
The development of automated lines for welding and the production of tools such as jigs and fixtures, therefore, requires great experience and skills, which are the prerogative of only a few companies in the world. One such company is Chropynska Slovakia, a Slovakian firm that counts globally important groups among its customers in sectors such as automotive, railways, aerospace, and agricultural machinery production.
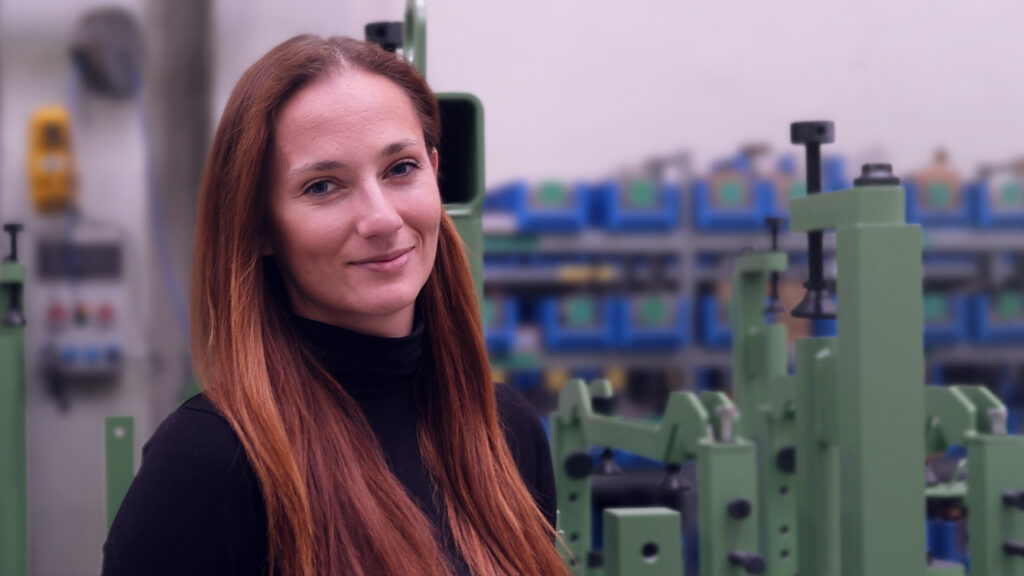
“With Twyn, we are optimistic about the future. The solution allows us to further enhance our production processes while maintaining the high quality of our products.”
Kristína Uhrínová, Quality Manager, Chropynska Slovakia
CONTROL WITH TABLETS
The company is located in Detva, in central Slovakia, about fifty kilometers north of the border with Hungary. For some time now, it has been equipped with an augmented reality solution to quickly verify the parts it produces or purchases from third parties against their 3D CAD models. They chose Twyn by Visometry, a mobile software platform for visual quality inspection, which allows manufacturers to create inspection plans and perform real-time checks with tablets, wherever components are produced or stored.
Kristína Uhrínová, Quality Manager at Chropynska Slovakia, explains how the solution is used in her company and highlights its advantages. “We use Twyn software extensively in the welding department,” she explains. “We check the correct position of all parts to be welded before beginning operations. It helps us locate items that are rotated, shifted, or missing from their intended position, a common problem in our line of manufacturing. It also allows us to simplify and speed up the inspection of elements welded together after machining, where we use Twyn in addition to traditional measurement solutions.”
The welding process is critical in many industries and requires verification of all production steps, each presenting different challenges. “Twyn has proven to be the ideal tool,” continues Kristína Uhrínová, “for a company like ours that aims to ensure 100% quality. Remakes are very expensive in our industry, and we have seen that augmented reality allows us to avoid them. Furthermore, we can document every phase of the process and share the documentation with other departments throughout the company.”
Using the Visometry augmented reality system for visual quality inspection on a product manufactured by Slavia Production Systems at its site in Detva, Slovakia.
INCOMING AND OUTGOING INSPECTIONS
But Chropynska Slovakia doesn’t just use AR solutions for welding. Twyn has also proven invaluable for “interoperative” control, i.e., between different production steps, and for inspecting incoming parts immediately after delivery by suppliers. Kristína Uhrínová explains, “Twyn’s ability to compare parts with their CAD specifications simplifies the definition of ‘quality gates,’ or control stations, throughout the production process. This helps us catch errors as soon as they occur, preventing downtime or costly rework. Quality inspections conducted with Twyn also optimize collaboration between companies by ensuring that manufactured parts meet CAD specifications before delivery, with an outbound inspection, or immediately after delivery, with an inbound inspection, but always at an early stage.”
Visometry allows immediate comparison between the manufactured part and its three-dimensional CAD model.
PARTS POSITIONING
Chropynska Slovakia is a leading manufacturer of jigs and fixtures, which facilitate welding operations and other processes by allowing easy positioning and alignment of the components to be welded or machined. Kristína Uhrínová adds, “Twyn proves to be invaluable even in this case because it enables real-time control and digital verification of the alignments between pieces, and necessary adjustments in the event of errors. We see immense potential in this Twyn application because it allows us to verify both the completeness and correctness of the entire assembly, helping us avoid errors and costly rework.”
According to the experts at Chropynska Slovakia, additional Twyn functions, such as Automatic Deviation Detection, will play an incresignly important role: Augmented reality allows deviations from the CAD drawing to be automatically highlighted in different colors, such as for attachment points or holes that are out of position.
Control of a chisel jig. Slavia Production Systems specialises in the design and manufacture of automated welding lines, for which it also produces all the ancillary parts.
EASY AND INTUITIVE
Chropynska Slovakia’s Quality Manager also highlights the main advantages of using Twyn. “This solution is fast and efficient, intuitive, and allows us to inspect both series productions and individual parts. In addition to immediately comparing components with their 3D CAD drawings, it can also check mirrored ones. We produce many ‘mirror’ pieces, but the technical documentation provided to the production department always contains only the drawing of the original parts. The workers must thus picture the mirrored parts in their minds during the inspection phases, risking undetected errors. Twyn performs this check automatically.”
Other strengths? “We really like the intuitive nature of this tool and the fact that inspections can be conducted at any point in the plant, avoiding unnecessary movements of parts to specific quality control areas,” concludes Kristína Uhrínová, the Quality Manager at Chropynska Slovakia.
The original Italian text written by Riccardo Oldani was published in Tecn’è Magazine.
Curious?
Start your free trial of Twyn and test the AR-powered inspection platform for 30 days.